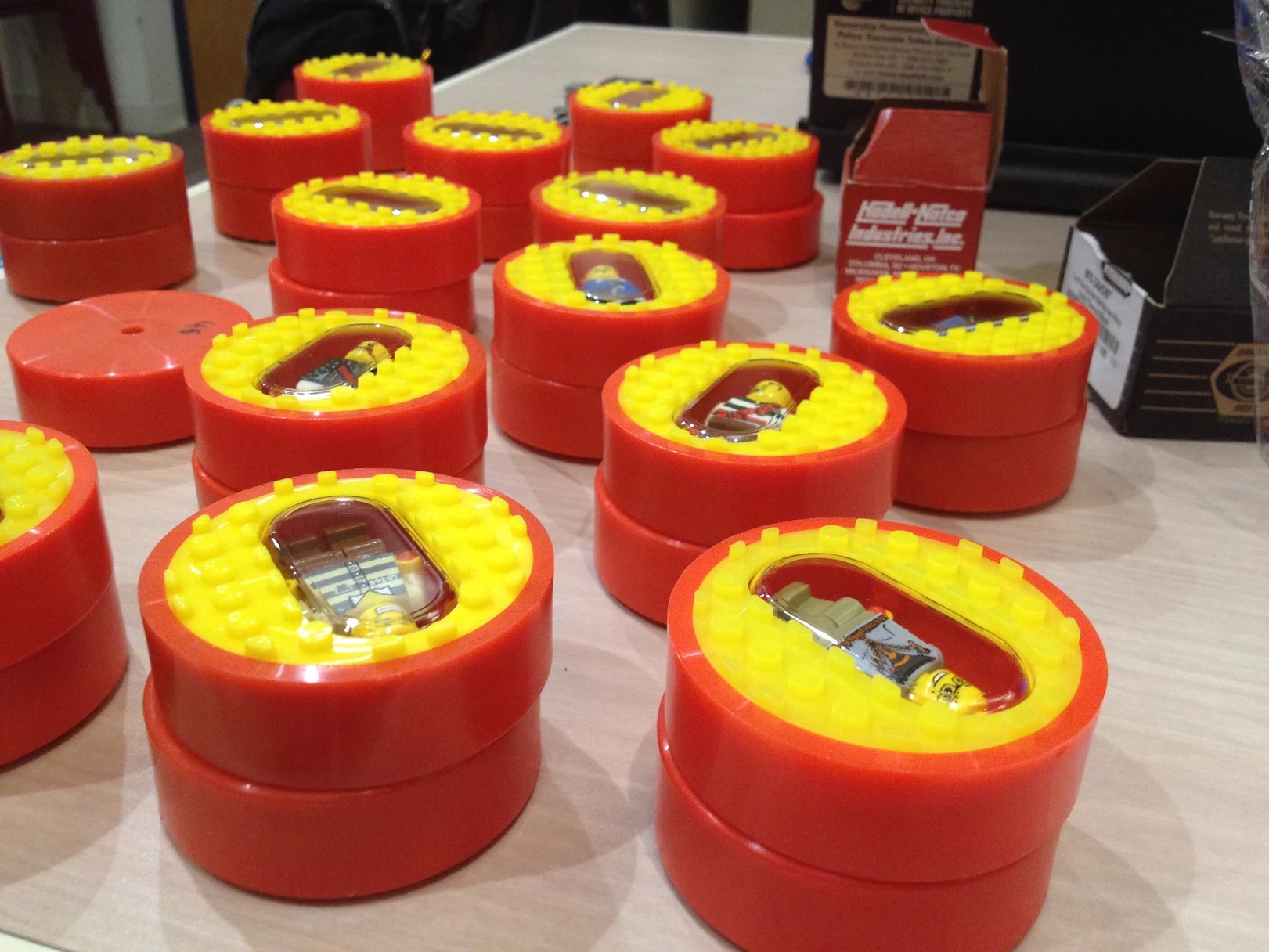
Background
Through 2.008 at MIT, our team designed and created 50 functional yo yo’s. Each yo yo consists of two body halves, two enclosing plates which can attach to lego bricks and through which a Lego minifig is visible, and a thermoformed bubble to keep the minifigs inside the yo yos.
We built molds for each part and used an injection molder to obtain our final models.
In my 2.008 course, my team was tasked with developing 50 yo yo’s which are both uniquely designed and functional as a toy.
Lessons Learned
- Team work and project management
- Optimizing products based on time, cost and quality
- Design for manufacturing and design for injection molding
- Machining, Injection Molding, MasterCAM, SolidWorks
My partner and I were responsible for the yellow, lego brick plates which would enclose snap into the body of the yo yo.

Yo Yo face plate which attached to Lego brand bricks and objects
Due to its many nubs, it would often stick in the injection molding machine and was thus unable to be ejected consistently. To counter this issue, we designed a trunk ring around the outside of the part to increase ejection force. Fundamentally, we learned that even if a single part works, producing it at scale is more difficult and that steps need to be taken to consider volume.
Our team’s summary video can be found here: 2.008 Team Minifig